Average Price of Siding Replacement
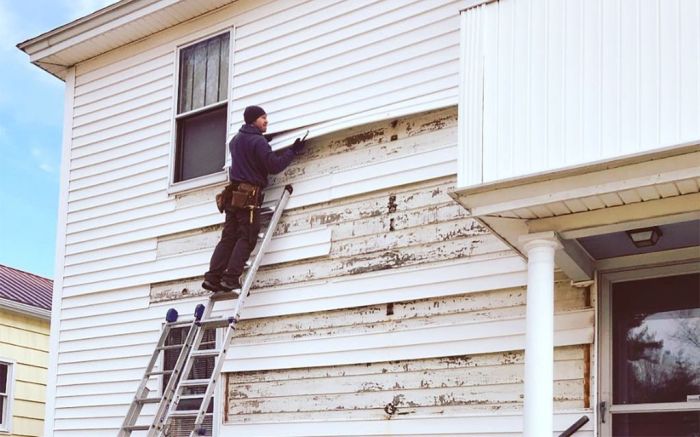
Average price of siding replacement varies wildly, depending on factors like your home’s size, the siding material you choose, and your location. This guide breaks down the costs, helping you budget for this significant home improvement project. We’ll explore different siding options, regional price differences, and potential hidden costs to ensure you’re fully prepared.
Understanding these factors is key to getting accurate estimates and avoiding unexpected expenses. From vinyl’s affordability to the longevity of fiber cement, we’ll compare materials and guide you through the process of finding a reliable contractor. Let’s dive in and get you siding-savvy!
Factors Influencing Siding Replacement Costs
Replacing your siding is a significant home improvement project, and the cost can vary widely. Several key factors influence the final price, making it crucial to understand these elements before starting your project. This will help you budget effectively and avoid unexpected expenses.
Siding Material Costs
The type of siding you choose significantly impacts the overall cost. Different materials offer varying levels of durability, aesthetics, and maintenance requirements, all of which affect the price per square foot and the overall installation cost.
Material | Average Cost per Square Foot | Pros | Cons |
---|---|---|---|
Vinyl | $3-$10 | Affordable, low maintenance, variety of colors and styles | Can be damaged easily, less durable than other options, may fade over time |
Wood | $7-$20+ | Classic look, durable if properly maintained, can increase home value | High maintenance (painting, staining), susceptible to rot and insect damage, expensive |
Fiber Cement | $8-$15+ | Durable, fire-resistant, low maintenance, long lifespan | More expensive than vinyl, can be brittle and prone to cracking during installation, requires professional installation |
Metal | $10-$25+ | Extremely durable, long lifespan, fire-resistant, low maintenance | Can dent, expensive, can be noisy in rain or hail |
Labor Costs and House Size
Labor costs are a significant portion of the total expense. The size of your house directly impacts the amount of time and labor required. A larger house will naturally require more siding, increasing both material and labor costs. The complexity of the job, such as the presence of multiple stories or intricate architectural details, also affects labor costs. Highly skilled labor, often needed for more complex projects, commands a higher price.
Regional Variations in Costs
The cost of siding replacement can vary significantly depending on your location. Factors such as the local cost of labor, material availability, and regional building codes all play a role. Areas with a higher cost of living or a shortage of skilled labor will typically have higher installation costs. For example, a siding replacement in a densely populated urban area might be more expensive than a similar project in a rural area.
Project Complexity and Repairs
The complexity of the project significantly impacts the cost. A simple replacement of existing siding with the same type of material requires less labor and is generally less expensive. However, if significant repairs are needed—such as replacing rotten wood, repairing damaged sheathing, or addressing water damage—the project becomes more complex and costly. These repairs add time and labor, increasing the overall expense.
Hypothetical Cost Comparison: Simple vs. Complex Replacement, Average price of siding replacement
Let’s consider two scenarios for a 1500 square foot house:
Scenario 1: Simple Vinyl Siding Replacement: This involves replacing existing vinyl siding with new vinyl siding of the same type. Assuming a cost of $5 per square foot for materials and $3 per square foot for labor, the total cost would be approximately $12,000 ($7,500 materials + $4,500 labor).
Scenario 2: Complex Siding Replacement with Repairs: This involves replacing old wood siding that is severely damaged and requires extensive repairs to the underlying sheathing and water damage. This scenario might require additional labor for repairs, potentially involving specialized tradespeople. The cost of materials could also increase due to the need for more specialized materials. In this case, the total cost could easily reach $25,000 or more, reflecting the added complexity and repair costs.
Regional Price Variations
Source: whatisvinyl.com
Siding replacement costs aren’t uniform across the United States. Several factors contribute to significant price differences between regions, making it crucial to understand these variations when budgeting for your project. These differences aren’t just minor fluctuations; they can represent thousands of dollars in total cost.
Regional differences in siding replacement costs stem primarily from three interconnected factors: labor costs, material availability and pricing, and local regulations and permitting processes. Higher labor costs in certain areas directly translate to higher overall project expenses. Similarly, the accessibility and cost of specific siding materials, influenced by transportation distances and local demand, also plays a significant role. Finally, local building codes and permitting requirements can add complexity and expense to the process.
Regional Cost Comparison
The table below presents a simplified overview of average siding replacement costs across different regions. Remember that these are broad estimates, and actual costs will vary depending on the specific project details.
Region | Average Cost (low) | Average Cost (high) | Contributing Factors |
---|---|---|---|
Northeast (e.g., New York, Massachusetts) | $10,000 | $25,000 | High labor costs, potential for complex historical building codes, higher material transportation costs. |
South (e.g., Texas, Georgia) | $8,000 | $18,000 | Generally lower labor costs compared to the Northeast, but material costs can vary depending on the specific type of siding chosen. |
Midwest (e.g., Illinois, Iowa) | $9,000 | $20,000 | Labor costs are moderate, and material availability is generally good, though transportation costs can still be a factor depending on location. |
West (e.g., California, Oregon) | $12,000 | $30,000 | High labor costs, potentially higher material costs due to transportation from distant sources, and stringent building codes in some areas. |
Significant Regional Discrepancies
Three regions illustrate the significant price disparities: the Northeast, the South, and the West Coast. The Northeast typically sees the highest costs due to a combination of high labor rates and potentially complex permitting processes associated with older homes. The South often has lower costs because of generally lower labor rates. However, this can be offset by increased material costs in certain areas. The West Coast experiences high costs, mirroring the Northeast, primarily due to high labor costs and the expense of transporting materials over long distances. These differences highlight the importance of obtaining local quotes before making any decisions.
Visual Representation of Price Variations
Imagine a map of the United States. The Northeast, including New England and parts of the Mid-Atlantic, is shaded a deep red, representing the highest average costs. The South, encompassing states like Texas, Louisiana, and Georgia, is shaded light orange, indicating lower average costs. The West Coast, from California to Oregon and Washington, is also shaded deep red, reflecting the high costs in those areas. The Midwest and the Plains states are shaded a light yellow-orange, showing a moderate range of costs. This color-coded map visually demonstrates the considerable regional variation in siding replacement costs.
Material-Specific Cost Analysis: Average Price Of Siding Replacement
Source: americanchoiceexteriors.com
Choosing the right siding material significantly impacts the overall cost of your replacement project. This section breaks down the price differences between popular options, considering both initial material costs and installation expenses. We’ll also examine long-term costs related to lifespan and maintenance.
Vinyl Siding Costs
Vinyl siding is a popular budget-friendly choice. Its affordability stems from its mass production and relatively simple installation. However, cheaper options may lack durability and fade faster.
- Cost Range: $3-$15 per square foot (material only), with installation adding another $2-$5 per square foot. This wide range reflects the vast differences in quality and features.
- Lifespan: 20-40 years, depending on quality and exposure to the elements. Lower-grade vinyl can fade or warp more quickly.
- Maintenance: Minimal. Generally requires only occasional cleaning with soap and water.
- Budget-Friendly Example: Basic, solid-color vinyl siding with simple profiles. This option prioritizes affordability over aesthetic features.
- High-End Example: Vinyl siding that mimics the look of wood shake or stone, often featuring more intricate profiles and a thicker gauge for increased durability and longevity. These options are significantly more expensive than basic vinyl but still generally less costly than other materials.
Wood Siding Costs
Wood siding offers a classic, natural look but comes with a higher price tag and increased maintenance demands. The cost varies greatly depending on the wood type (cedar, redwood, etc.) and the complexity of the installation.
- Cost Range: $10-$30+ per square foot (material only), with installation costing an additional $5-$15 per square foot. Exotic hardwoods will significantly increase the cost.
- Lifespan: 30-50 years or more with proper maintenance. However, untreated wood is susceptible to rot, insect damage, and moisture issues.
- Maintenance: High. Requires regular painting or staining to protect it from the elements and prevent deterioration. Regular inspections for damage are also necessary.
- Budget-Friendly Example: Pressure-treated pine or fir siding, which is more affordable than cedar or redwood but may require more frequent maintenance.
- High-End Example: Premium cedar or redwood siding, often with a custom finish or intricate detailing. These options demand higher initial investment but can last for many decades with appropriate care.
Fiber Cement Siding Costs
Fiber cement offers a durable, low-maintenance alternative to wood, mimicking its look without the drawbacks of rot or insect infestation. However, it is more expensive than vinyl.
- Cost Range: $8-$20+ per square foot (material only), with installation adding $5-$10 per square foot. The cost varies based on the thickness, texture, and style of the siding.
- Lifespan: 50 years or more with minimal maintenance. Its resistance to fire, moisture, and insects makes it a long-lasting option.
- Maintenance: Low. Requires occasional cleaning and repainting every 10-15 years, depending on the climate and exposure.
- Budget-Friendly Example: Standard fiber cement panels in a neutral color with a simple profile.
- High-End Example: Fiber cement siding that replicates the appearance of natural stone or brick, often with textured surfaces and intricate details. These options command a higher price but offer superior aesthetics and durability.
Metal Siding Costs
Metal siding, typically aluminum or steel, is known for its extreme durability and longevity. However, it can be more expensive upfront than vinyl or fiber cement, and the installation process can be more complex.
- Cost Range: $7-$25+ per square foot (material only), with installation costing $4-$12 per square foot. The cost depends on the metal type, finish, and gauge.
- Lifespan: 50+ years with minimal maintenance. Metal siding is highly resistant to damage from weather, insects, and fire.
- Maintenance: Very low. Requires only occasional cleaning. However, dents or scratches may be more visible than on other siding materials.
- Budget-Friendly Example: Basic aluminum siding in a solid color.
- High-End Example: Steel siding with a high-quality finish that mimics the appearance of wood or stone, or features unique colors and textures.
Labor Costs and Contractor Selection
Choosing the right contractor significantly impacts your siding replacement project’s overall cost and success. Labor represents a substantial portion of the total expense, and understanding the factors influencing these costs is crucial for budgeting and making informed decisions. This section explores labor cost variations, contractor selection strategies, and the importance of thorough planning.
Labor costs for siding replacement are influenced by several key factors. The contractor’s experience and reputation directly affect their hourly or project rates. Highly experienced and reputable contractors often command higher fees, reflecting their expertise and the likelihood of a higher-quality, more efficient job. Geographical location also plays a role; labor costs in high-demand areas with a higher cost of living tend to be higher than in less populated regions. Finally, project complexity – such as the size of the house, the type of siding, the need for extensive repairs or removal of existing siding, and intricate detailing – all contribute to increased labor time and therefore, higher costs.
Contractor Selection Strategies
Finding a reputable and reasonably priced contractor involves a multi-step process. Begin by gathering recommendations from friends, family, or neighbors who have recently undertaken similar projects. Online resources, such as review websites and contractor directories, can also provide valuable information and potential leads. Always check licensing and insurance; a licensed and insured contractor provides legal protection and assurance of professional standards. Thoroughly review online reviews, paying attention to both positive and negative feedback to gauge the contractor’s reliability and customer service. Remember to verify references, directly contacting previous clients to inquire about their experiences with the contractor.
General Contractor vs. Specialized Siding Installer
The choice between a general contractor and a specialized siding installer depends on the scope of your project. General contractors manage various aspects of construction projects, including siding installation. They may subcontract the siding work to a specialist, adding a layer of management fees to the overall cost. Specialized siding installers, on the other hand, focus solely on siding and often possess greater expertise in this specific area. They may offer competitive pricing due to their specialization and streamlined operations. For straightforward siding replacements, a specialized installer might be more cost-effective. For larger projects involving multiple aspects of home renovation, a general contractor may be a more suitable choice, offering a single point of contact for the entire project.
Importance of Multiple Quotes and Contract Review
Obtaining multiple quotes from different contractors is essential for comparing prices and services. This allows you to identify fair pricing and avoid overpaying. Before committing to a contractor, thoroughly review the contract, ensuring all aspects of the project, including materials, labor, payment schedules, warranties, and cleanup procedures, are clearly defined. Clarify any ambiguities and ensure you understand all the terms and conditions before signing. A well-written contract protects both you and the contractor, minimizing potential disputes and misunderstandings during the project. For example, a contract should specify the payment schedule, perhaps 25% upfront, 50% upon completion of the majority of work, and 25% upon final inspection and approval. This prevents the contractor from demanding full payment before the work is complete.
Hidden Costs and Unexpected Expenses
Source: thumbtack.com
Siding replacement, while a significant investment in your home’s curb appeal and protection, often involves costs beyond the initial estimate. Understanding these potential hidden expenses is crucial for budgeting accurately and avoiding unpleasant financial surprises during the project. Failing to account for these can lead to project delays, budget overruns, and even compromise the quality of the finished work.
Unexpected expenses can significantly impact your siding replacement budget. These unforeseen costs often stem from issues discovered only during the demolition or installation phases. For example, rotten wood beneath the siding might require extensive repairs, or unexpected complications with the underlying structure could necessitate additional labor and materials. Preparing for such contingencies is essential to ensure a smooth and financially manageable renovation.
Permitting and Inspections
Securing necessary permits and undergoing inspections are often overlooked aspects of siding replacement. Permits, which vary in cost depending on your location and the scope of the project, are legally required in most areas before work can begin. Inspections ensure the work meets building codes and safety standards, and failing to pass an inspection can lead to delays and added costs for rework. Budgeting for these upfront fees prevents unexpected delays and potential fines.
Demolition and Waste Removal
The removal of old siding and underlying materials can be surprisingly labor-intensive and expensive. If the old siding contains asbestos or lead paint, specialized removal and disposal procedures, which incur significant extra costs, are required. Furthermore, waste disposal fees, depending on the volume of materials and local regulations, can add up considerably. Accurately estimating these costs requires a thorough assessment of the existing siding and a plan for efficient waste management.
Underlying Structural Issues
During demolition, unforeseen structural problems like rotted sheathing, damaged framing, or insect infestation might be uncovered. Addressing these issues is critical for a long-lasting siding job, but it significantly increases both labor and material costs. A pre-project inspection by a qualified professional can help identify and mitigate some of these risks, reducing the likelihood of unexpected expenses.
Unforeseen Material Needs
The initial material estimate might not account for all necessary components. Unexpected issues, such as needing extra flashing, trim, or sealant, can add up. Also, unforeseen variations in the existing structure might necessitate adjustments to the material quantities, resulting in additional costs. Always request a detailed breakdown of materials from your contractor and allow for a contingency buffer in your budget.
Potential Hidden Costs and Mitigation Strategies
It’s crucial to proactively address potential hidden costs. A comprehensive approach involves detailed planning and communication with your contractor.
- Permits and Inspections: Inquire about permit fees early in the process and factor them into your budget. Schedule inspections well in advance to avoid delays.
- Demolition and Waste Removal: Get multiple quotes for demolition and waste disposal, and ensure they include the costs of handling hazardous materials if necessary.
- Underlying Structural Issues: Consider a pre-project inspection to identify potential problems and incorporate the associated costs into your budget.
- Unforeseen Material Needs: Request a detailed material list from your contractor, and add a contingency of 10-15% to your material budget to account for unexpected needs.
- Contractor Fees: Clarify all contractor fees upfront, including travel expenses, change orders, and potential overtime charges.
Concluding Remarks
Replacing your siding is a substantial investment, but with careful planning and research, you can achieve a beautiful and durable exterior while staying within your budget. Remember to factor in all potential costs – from materials and labor to permits and unforeseen issues. By comparing quotes, understanding material lifespans, and selecting a reputable contractor, you’ll be well-equipped to make informed decisions and enjoy your newly sided home for years to come.
Comments are closed.