How Much Does Siding Cost?
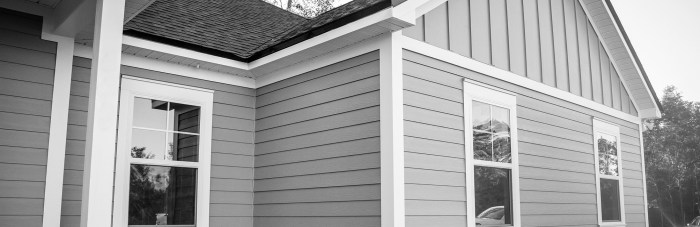
How much does siding cost? That’s the million-dollar question (or maybe the ten-thousand-dollar question!), and the answer isn’t simple. The price of new siding depends on a surprising number of factors, from the type of material you choose to the size and complexity of your house. We’ll break down all the cost components – materials, labor, regional differences, and more – so you can get a realistic estimate for your project. Understanding these factors will empower you to make informed decisions and avoid unexpected expenses.
This guide will walk you through everything you need to know to budget effectively for your siding project. We’ll explore the cost variations between different siding materials like vinyl, wood, fiber cement, and metal, detailing their lifespans and maintenance needs. We’ll also delve into labor costs, regional pricing differences, and those often-overlooked extras like permits and potential repairs. By the end, you’ll have a much clearer picture of what to expect and how to find a reputable contractor to bring your vision to life.
Factors Affecting Siding Cost
Source: modern-exterior.com
Several key factors significantly influence the overall cost of your siding project. Understanding these factors will help you budget effectively and make informed decisions about materials and installation. The most significant factor is the choice of siding material itself, but labor costs, project complexity, and regional variations also play a crucial role.
Siding Material Costs
The type of siding you choose dramatically impacts the final price. Different materials offer varying levels of durability, aesthetic appeal, and maintenance requirements, all of which affect cost. Let’s compare some popular options: vinyl, wood, fiber cement, and metal.
Siding Material | Average Price per Square Foot | Lifespan (Years) | Maintenance Requirements |
---|---|---|---|
Vinyl | $3 – $10 | 20-40 | Low; occasional cleaning |
Wood | $8 – $25+ | 20-50+ (depending on wood type and maintenance) | Moderate to High; regular painting, staining, and potential repairs |
Fiber Cement | $10 – $20+ | 50+ | Low to Moderate; occasional cleaning, repainting may be needed after many years |
Metal | $10 – $30+ | 50+ | Low; occasional cleaning, potential repainting depending on finish |
These price ranges are averages and can vary widely based on factors like the specific product, region, and installer. For instance, premium vinyl siding with enhanced features will cost more than basic vinyl. Similarly, exotic wood siding will be significantly pricier than standard cedar.
Labor Costs and Project Complexity
Labor costs are a substantial portion of the overall siding project expense. The complexity of the project – including the size of your house, the number of architectural details (like dormers and bay windows), and the need for extensive repairs or removal of existing siding – will all affect the labor hours required, and therefore the cost. A simple, straightforward installation on a single-story home will be cheaper than a complex project on a multi-story house with intricate detailing. Furthermore, regional differences in labor rates will also influence the total cost. For example, labor costs in a major metropolitan area are generally higher than in rural areas.
Regional Variations in Pricing
Material and labor costs fluctuate across different regions. Supply and demand, local regulations, and the availability of skilled labor all contribute to these variations. For instance, the cost of cedar siding might be lower in regions with abundant cedar forests, while areas prone to extreme weather might see higher demand for durable materials like fiber cement, driving up prices.
Labor Costs
Labor costs are a significant portion of your overall siding project expense, often rivaling or exceeding the material costs. Many factors influence the final labor bill, making it crucial to understand these variables before beginning your project. A clear understanding will help you budget effectively and avoid unexpected expenses.
Labor costs for siding installation are influenced by several key factors. These include the complexity of the job (new construction versus replacement), the size and accessibility of the house, the type of siding chosen (vinyl is generally faster to install than wood or fiber cement), the installer’s experience and location, and prevailing local wage rates. The condition of the existing structure also plays a role; extensive repairs or rotted wood will increase labor time and thus cost. Finally, the time of year can also affect labor rates, with peak seasons often commanding higher prices due to increased demand.
Hourly Rates for Siding Installers
Hourly rates for siding installers vary significantly across different regions of the country and even within a single region. While national averages are difficult to pin down due to these regional disparities, a reasonable estimate for experienced installers would range from $40 to $80 per hour, depending on the aforementioned factors. Rural areas may have slightly lower rates, while major metropolitan areas tend to command higher prices. Unskilled labor, such as helpers, might cost less, ranging from $20 to $40 per hour. These are estimates, and it’s crucial to get multiple quotes from local contractors to establish an accurate cost for your specific project.
Labor Costs: New Construction vs. Replacement
New construction siding projects generally require less labor than replacement projects. In new construction, the walls are typically clean and prepared for installation, simplifying the process. Replacement projects often involve removing old siding, repairing underlying sheathing or damage, and addressing potential issues like moisture damage or pest infestations, all adding to labor time. For example, a new construction project might require only 100 labor hours for a medium-sized house, whereas a comparable replacement project might necessitate 150-200 hours due to the additional preparation and repair work.
Labor Cost Breakdown
The total labor cost is typically broken down into three main phases: preparation, installation, and cleanup. The proportion of time spent on each phase varies depending on the project’s specifics.
Phase | Percentage of Total Labor Time (Estimate) | Description |
---|---|---|
Preparation | 20-30% | This includes surface preparation, such as removing old siding, repairing damaged areas, installing flashing and other underlayments, and ensuring a proper substrate for the new siding. |
Installation | 60-70% | This is the core of the project, involving the actual installation of the new siding, ensuring proper alignment, and securing it to the house. |
Cleanup | 10-20% | This involves removing debris, disposing of waste materials responsibly, and ensuring the worksite is left clean and tidy. |
Project Size and Complexity
The overall cost of your siding project isn’t just about the type of siding you choose; it’s heavily influenced by the size and complexity of your home and the amount of prep work required. A larger house naturally needs more siding, leading to higher material costs. Similarly, intricate architectural details and the condition of your existing siding significantly impact the labor involved and, consequently, the final price.
The square footage of your home’s exterior walls is the primary driver of material costs. A simple, single-story ranch will require far less siding than a two-story Victorian with numerous dormers and gables. Beyond square footage, the complexity of your home’s design introduces significant variables. Features like intricate trim work, multiple rooflines, or numerous windows and doors increase both material and labor costs. For example, installing siding around dormers often involves more cuts and specialized techniques, increasing labor time. Similarly, gables, with their angled surfaces, demand more precise measurements and careful installation to ensure a clean, watertight finish.
Architectural Features and Cost Increases
Adding architectural elements like dormers and gables increases siding costs. Dormers, those windowed projections from a roof, require meticulous measurements and careful installation around the window frames and roofline. This added precision and the extra material needed to cover the dormer’s unique angles increase labor costs. Gables, triangular sections of wall at the end of a roof slope, also present challenges. The angled surfaces require more cuts and fitting, adding to both material and labor expenses. Consider a two-story house with multiple gables and dormers; the increased complexity translates to a substantially higher cost compared to a simple rectangular house of the same square footage. For instance, a simple ranch might cost $10,000 for siding, while a similar-sized house with extensive gables and dormers could easily cost $15,000 or more.
Preparation Work and its Impact
The condition of your existing siding and the amount of preparatory work needed heavily influence the total project cost. Removing old, damaged siding is often a significant part of the project. If the old siding is asbestos-containing material (ACM), specialized removal and disposal procedures are necessary, adding substantial costs. Furthermore, if the underlying sheathing needs repair or replacement due to rot or damage, this adds considerable time and expense. Repairing damaged areas before installing new siding is crucial to prevent future problems. This prep work might involve replacing damaged wood, patching holes, or addressing water damage. The extent of this preparation work directly affects the overall labor costs, which can sometimes exceed the cost of the siding material itself. For example, a project involving extensive rot repair could add 30-50% to the overall cost.
Project Complexity and Cost Increase
The following table illustrates how different levels of project complexity can impact the total siding cost, assuming a 1500 sq ft house with standard siding material. These are estimates, and actual costs will vary depending on location and specific circumstances.
Project Complexity | Estimated Cost Increase (%) | Example |
---|---|---|
Simple, no prep work needed | 0% | Single-story ranch, good condition, siding removal |
Moderate complexity, some prep work | 10-20% | Two-story house, minor repairs to existing sheathing |
High complexity, significant prep work | 30-50% | Two-story house with multiple gables, extensive rot repair, ACM removal |
Very High complexity, extensive prep and specialized features | 50-75% | Large Victorian home with intricate trim, dormers, gables, significant structural repairs, and ACM removal. |
Regional Variations in Pricing
Siding costs aren’t uniform across the United States. Several factors contribute to significant price differences between regions, impacting both the materials and the labor involved in installation. These variations can make a substantial difference in your overall project budget.
Geographical location plays a crucial role in determining the final cost of your siding project. Labor rates, material availability and transportation costs, and even the prevalence of specific siding types all vary considerably depending on where you live. For instance, areas with a high cost of living generally have higher labor rates, directly increasing the overall project expense. Conversely, regions with abundant local material sources may see lower material costs.
Regional Cost Comparison
The table below provides a general overview of average siding costs across different regions. Remember that these are estimates and actual costs can vary based on the specific type of siding, project size, and other factors discussed previously. It’s always best to obtain multiple quotes from local contractors for accurate pricing.
Region | Average Siding Cost per Square Foot (USD) | Factors Contributing to Cost |
---|---|---|
Northeast (e.g., New England) | $8 – $15 | High labor costs, potential for harsh weather impacting installation, higher demand for durable siding options. |
Southeast (e.g., Florida, Georgia) | $7 – $12 | Lower labor costs compared to the Northeast, readily available materials in some areas, prevalence of impact-resistant siding due to hurricane risk. |
Midwest (e.g., Illinois, Ohio) | $7 – $13 | Moderate labor costs, varied material availability depending on specific location, common use of vinyl and fiber cement siding. |
Southwest (e.g., Arizona, Texas) | $7 – $14 | Labor costs can vary significantly within the region, with higher demand for heat-resistant and low-maintenance siding. |
West Coast (e.g., California, Oregon) | $9 – $16 | High labor costs, potentially higher material costs due to transportation, increased demand for fire-resistant siding in certain areas. |
Permits and Inspections
Getting the necessary permits and inspections for your siding project is crucial. Failing to do so can lead to fines, delays, and even the need to redo work. The costs associated with these processes can vary significantly depending on your location and the size of the project. Understanding these costs upfront is essential for accurate budgeting.
Permitting and inspection fees are determined by local governments (city, county, or municipality). These fees cover the administrative costs of processing your application and conducting inspections to ensure your project meets building codes and regulations. The complexity of your siding project, such as the size of the area being sided or the type of siding material used, will also influence the permit cost. For instance, a large commercial building project will incur significantly higher fees than a small residential project. In addition to the permit application fee, you might encounter inspection fees for each stage of the project, such as the initial inspection before work begins, a mid-project inspection, and a final inspection upon completion.
Permit Fees Vary by Location and Project Scope
Permit fees are not standardized across the country. A simple siding job on a small house in a rural area might only cost a few hundred dollars, while a larger project in a major city could cost several thousand. Factors contributing to the variance include the size of the project, the type of siding used, and local regulations. For example, some areas might require more stringent inspections for certain types of siding materials, leading to higher fees. It’s advisable to contact your local building department to obtain an accurate estimate of permit fees based on your specific project. They can provide a detailed breakdown of fees and explain any unique requirements for your area.
Examples of Permit Requirements and Associated Costs
Let’s consider a few examples. In a hypothetical suburban area, a permit for replacing siding on a single-family home might cost between $200 and $500, including inspection fees. This price range accounts for relatively straightforward projects with standard materials. However, if the project involves significant structural modifications or the use of specialized materials, the costs could easily climb to $1000 or more. A larger commercial building project, say, a multi-story office building, could easily have permit fees exceeding $5000, depending on the project’s scope and the local regulations. Always check with your local authority for accurate cost information.
Typical Permit and Inspection Fees
The following table provides a general overview of typical permit and inspection fees. Keep in mind that these are estimates and can vary significantly depending on location and project specifics. Always consult your local building department for precise cost information.
Project Type | Permit Fee (Estimate) | Inspection Fees (Estimate) | Total Estimated Cost |
---|---|---|---|
Small residential siding replacement | $200 – $500 | $100 – $300 | $300 – $800 |
Large residential siding replacement | $500 – $1500 | $200 – $600 | $700 – $2100 |
Commercial building siding | $1000 – $5000+ | $500 – $2000+ | $1500 – $7000+ |
Additional Costs: How Much Does Siding Cost
Source: mcclellandsroofing.com
Getting new siding is rarely a simple, straightforward process. While the base cost of materials and labor is a significant portion of the total expense, several other factors can significantly inflate your final bill. Understanding these potential added expenses is crucial for accurate budgeting and avoiding unpleasant surprises during your project. Failing to account for these extras can lead to project delays or even force you to compromise on the quality of materials or workmanship.
It’s important to remember that these additional costs are not always predictable, and their magnitude can vary greatly depending on the specifics of your home and the condition of your existing siding. Therefore, building a buffer into your budget is always a wise move.
Old Siding Removal, How much does siding cost
Removing existing siding adds both time and labor to the project. If your old siding is in good condition and can be left in place, this cost can be avoided. However, damaged, rotting, or asbestos-containing siding must be removed and disposed of properly, often requiring specialized handling and disposal fees. The cost depends on the type of siding, its condition, and the size of the house. For example, removing old wood clapboard siding will typically be more expensive and time-consuming than removing vinyl siding. A large two-story home will cost more than a small bungalow. Expect to pay anywhere from $1 to $5 per square foot for removal, depending on these factors.
Underlying Structure Repairs
Once the old siding is removed, the underlying structure of your home’s exterior will be exposed. This often reveals problems that need to be addressed before new siding can be installed. This could include rotted wood, damaged sheathing, insect infestation, or even structural issues. Repairing these problems can add significantly to the overall cost, potentially running into thousands of dollars depending on the extent of the damage. For instance, replacing a section of rotted sheathing might cost a few hundred dollars, while repairing extensive water damage could cost several thousand.
Trim Work
Installing new siding often involves significant trim work. This includes replacing or repairing window and door casings, corner boards, fascia boards, and other trim elements. The complexity and cost of this work depend on the style and detail of the trim, as well as the condition of the existing trim. Intricate, custom millwork will be more expensive than simpler, standard trim pieces. Consider this cost a significant variable, potentially ranging from a few hundred dollars to several thousand, depending on the scope of the work.
Painting
While not always necessary, many homeowners choose to paint their new siding. This adds another layer of cost to the project, dependent on the size of the house, the number of coats required, and the type of paint used. Painting can easily add several hundred to several thousand dollars to the total cost. For example, a two-story house might cost between $2,000 and $5,000 to paint depending on the type of paint and labor rates.
Unexpected Costs
Unexpected issues frequently arise during siding projects. These could include discovering hidden damage, encountering unforeseen material shortages, or experiencing weather delays. It’s prudent to allocate a contingency budget of 10-20% of the estimated total cost to cover such unforeseen expenses. For example, on a $10,000 siding project, a 15% contingency would mean setting aside an additional $1,500.
Table of Additional Costs
Additional Cost | Potential Cost Range | Impact on Overall Budget |
---|---|---|
Old Siding Removal | $1-$5 per square foot | Significant, especially with large homes or difficult-to-remove siding |
Underlying Structure Repairs | Hundreds to thousands of dollars | Highly variable, potentially substantial |
Trim Work | Hundreds to thousands of dollars | Significant, depending on complexity and extent of work |
Painting | Hundreds to thousands of dollars | Significant, dependent on house size and paint choice |
Unexpected Costs (Contingency) | 10-20% of total estimated cost | Crucial for avoiding budget overruns |
Estimating and Budgeting
Getting an accurate estimate for your siding project is crucial to avoid unexpected costs and ensure a smooth process. There are several methods you can use to arrive at a realistic budget, and understanding these methods will empower you to make informed decisions. This section will explore different estimation techniques and guide you through building a comprehensive budget.
Methods for Estimating Siding Installation Costs
Several approaches can help you estimate siding costs. The simplest is using a rough cost per square foot, which you can find online or through local contractors. However, this method lacks detail and may not account for project specifics. A more accurate approach involves obtaining detailed quotes from multiple contractors. This allows for comparison and ensures you’re getting a fair price. Remember, always get multiple quotes to avoid overpaying. Finally, you can perform a detailed cost breakdown yourself, which will be discussed in the next section. This allows for a highly personalized estimate, but requires more time and research.
Creating a Realistic Budget for a Siding Project
Creating a realistic budget involves more than just estimating the cost of materials and labor. You need to consider all potential expenses, including unforeseen circumstances. Start by gathering information about the project scope, including the area to be sided, the type of siding, and any necessary repairs or prep work. Next, obtain multiple detailed quotes from reputable contractors. Compare these quotes carefully, paying attention to the breakdown of costs (materials, labor, permits, etc.). Factor in a contingency buffer of 10-20% to account for unexpected expenses. Finally, ensure your chosen contractor provides a detailed contract that outlines all costs and project timelines.
Example of a Detailed Cost Breakdown
Let’s consider a hypothetical project: siding a 1,500 square foot house with vinyl siding.
Cost Item | Quantity/Details | Unit Cost | Total Cost |
---|---|---|---|
Vinyl Siding | 1,500 sq ft | $5/sq ft | $7,500 |
Labor | 1,500 sq ft | $3/sq ft | $4,500 |
Underlayment | 1,500 sq ft | $1/sq ft | $1,500 |
Permits | $500 | $500 | |
Waste Removal | $200 | $200 | |
Contingency (15%) | $1,925 | ||
Total Estimated Cost | $16,125 |
Note: These prices are examples and may vary significantly depending on your location, chosen materials, and contractor.
Steps Involved in Creating a Siding Project Budget
Planning is key to a successful project. A structured approach ensures you don’t overlook crucial aspects.
Step | Description |
---|---|
1. Determine Project Scope | Measure the area needing siding, identify siding type, and note any required repairs. |
2. Research Material Costs | Obtain quotes from multiple suppliers for siding, underlayment, and other materials. |
3. Get Contractor Quotes | Request detailed quotes from at least three reputable contractors, comparing labor costs and timelines. |
4. Account for Permits and Inspections | Inquire about permit costs and any inspection fees. |
5. Include Contingency Funds | Allocate 10-20% of the estimated cost to cover unexpected expenses. |
6. Create a Detailed Budget | Compile all costs into a single document for a clear overview. |
7. Review and Adjust | Regularly review and adjust the budget as needed, based on new information or changes to the project. |
Finding Reliable Contractors
Source: exteriorheroes.com
Finding the right siding contractor is crucial for a successful project. A poorly chosen contractor can lead to shoddy workmanship, cost overruns, and significant headaches. Taking the time to thoroughly vet potential contractors will save you stress and money in the long run.
Choosing a siding contractor involves more than just comparing prices. You need to assess their experience, qualifications, insurance coverage, and customer reviews to ensure they are capable of handling your project to your satisfaction. Remember, the lowest bid isn’t always the best deal; prioritize quality and reliability.
Contractor Licensing and Insurance
It’s essential to verify that any contractor you consider is properly licensed and insured. Licensing demonstrates that they’ve met minimum standards of competency within your area. Insurance protects you from liability in case of accidents or damages during the project. Contact your local licensing board to verify a contractor’s license status and confirm their insurance coverage details, including workers’ compensation and general liability insurance. Don’t hesitate to ask for proof of insurance certificates. This simple step can save you from substantial financial burdens in the event of unforeseen circumstances.
Checking References and Reviews
Before hiring, request references from previous clients and check online reviews on platforms like Google My Business, Yelp, and the Better Business Bureau. Contacting past clients directly allows you to get firsthand accounts of their experiences, including the contractor’s professionalism, responsiveness, and the quality of their work. Online reviews offer a broader perspective, though it’s important to be aware that not all reviews are genuine or unbiased. Look for consistent patterns in positive and negative feedback to gain a clearer picture of the contractor’s reputation. Pay attention to how the contractor responds to negative reviews; this can reveal their communication style and problem-solving abilities.
Evaluating Contractor Experience and Qualifications
Assess a contractor’s experience by inquiring about the types of siding projects they’ve completed, their years in business, and the size and complexity of past jobs. Ask for photos or examples of their previous work to evaluate the quality of their craftsmanship. Inquire about their familiarity with different siding materials and installation techniques relevant to your project. A contractor with extensive experience and a proven track record is more likely to deliver a high-quality outcome and manage the project efficiently. Don’t hesitate to ask for detailed information on their experience with projects similar to yours.
Questions to Ask Potential Contractors
Preparing a list of questions to ask potential contractors is a vital step in the selection process. This helps you gather the necessary information to make an informed decision. These questions should cover various aspects of the project, including the contractor’s experience, licensing, insurance, pricing, timeline, and warranty.
- Are you properly licensed and insured to perform siding work in my area?
- Can you provide references from previous clients?
- How long have you been in business, and what is your experience with [type of siding] installation?
- Can you provide examples of your previous work, including photos or addresses?
- What is your process for handling potential problems or delays during the project?
- What is your payment schedule, and what are your warranty terms?
- Do you have a detailed written contract outlining the scope of work, materials, and timeline?
- What is your estimate for the total cost of the project, including materials and labor?
- What is your estimated timeline for completing the project?
- What is your plan for cleanup and waste disposal?
Getting Multiple Bids and Comparing Quotes
Obtaining multiple bids from different contractors is essential for ensuring you receive competitive pricing and a fair assessment of the project’s scope. Compare not only the total cost but also the details of each quote, including the materials used, the labor costs, and the project timeline. Be cautious of bids that are significantly lower than others; this could indicate a compromise in quality or a lack of transparency in pricing. Thoroughly review each quote to ensure it aligns with your expectations and includes all necessary components. This comparative analysis will empower you to make a well-informed decision.
Epilogue
So, how much *does* siding cost? While there’s no single answer, this guide has equipped you with the knowledge to arrive at a personalized estimate. Remember to consider all factors – material choice, labor costs, regional variations, and potential add-ons – when budgeting. By getting multiple bids from reputable contractors and carefully planning your project, you can confidently tackle your siding upgrade, transforming your home’s exterior and increasing its value.
Comments are closed.